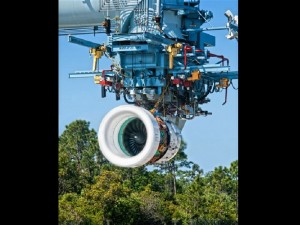
The Pratt & Whitney 1524G PurePower geared turbofan engine, being test-run in Florida. The lower weight is helping the engine provide a 15% reduction in fuel consumption and well as a 15% reduction in carbon emissions. AP
Planes are being built out of the same lightweight materials used for Formula 1 race cars. Their engines are being redesigned to squeeze more thrust out of every bit of fuel. And governments are developing air-traffic systems that will allow airlines to fly shorter routes.
Those and other advances have positioned airlines for the biggest gains in fuel efficiency since the dawn of the jet age in 1958. For airlines, more efficient jets will reduce their biggest expense. For passengers, it means fares won’t jump around as much with the price of oil.
“We’re seeing 25 years of improvements compressed into 10 years,” says Hans Weber, president of TECOP International, an aviation consulting firm.
Airlines’ urgency to reduce fuel use is being driven by two trends: soaring oil prices and tougher environmental regulations.
Pressured by airline executives for improvements, manufacturers have pushed the frontiers of technology by building lighter planes and borrowing essential engine-design advances from the auto industry, like automatic transmissions.
Airplane manufacturers have already reduced fuel consumption twice as much as car and train manufacturers have. In 1980, it took an average of 46 gallons (174 liters) of fuel to fly a passenger 1,000 miles (1,600 kilometers). Today, it takes 22 gallons (83 liters), according to an AP analysis of Department of Transportation data. Experts say the coming improvements could bring that number below 18 within a decade.
That can’t come soon enough for airlines struggling with the rising price of oil.
U.S. airlines lost a combined $1 billion in the first three months of this year, in large part because of a 24 percent spike in fuel costs. A decade ago, fuel accounted for 15 percent of an airline’s operating budget. Today, it’s 35 percent.
U.S. carriers with European routes face hundreds of millions of dollars a year of additional costs pegged to their fuel consumption starting next year, when the European Union begins limiting how much carbon dioxide airlines are allowed to emit before paying a penalty. The restrictions are expected to cost airlines worldwide $3.3 billion a year. The U.S. airlines are fighting the law in European courts.
With billions of dollars of aircraft and engine orders at stake, manufacturers are turning designs that were dreams only a few years ago into reality.
Boeing and Airbus are both building long-range jets — the 787 Dreamliner and A350, respectively — with half of their bodies made of carbon-fiber composites. The carbon-fiber weighs 20 percent less than traditional aluminum alloy.
But the real revolution will come from the way planes are powered.
Pratt & Whitney and CFM, a joint venture between General Electric and Safran, are unveiling engines that promise to cut fuel use by 15 percent. These engines are designed for single-aisle planes, which account for more than 75 percent of the 22,000 jets worldwide. The engines should save more than $1 million per aircraft per year.
“For the first time, we’re seeing a propulsion horserace,” says Richard Aboulafia, an analyst with the Teal Group.
The PurePower engine from Pratt & Whitney will debut on the new Bombardier CSeries in 2013. Its main technological advance is to add gears — similar to a car’s transmission — that will allow different parts of the engine to operate at different speeds. That boosts fuel efficiency and provides the same amount of power as a traditional engine but in smaller, lighter housing.
The LEAP-X from CFM has advancements in air flow and temperature-resistant coatings that allow the air passing through the engine core to be at temperatures otherwise hot enough to melt the surrounding metal. Those higher temperatures allow the engine to be more efficient.
Airbus is redesigning its A320 jets to accommodate both engines and says its A320neo, which starts flying in 2016, will cut fuel consumption by 20 percent. Airbus has already received more than 1,000 orders and commitments for future orders.
Boeing plans to offer the new engines on a single-aisle jet but has yet to decide whether it will update the 737, its best-seller, to accommodate them or design a new plane.
Other ways airlines will save on fuel:
— A satellite-based air traffic control system in the U.S., several years away, that could cut fuel consumption by 12 percent. Airlines and the government are fighting over who will pay for it. The current system is based on less precise World War II-era radar, which can force planes to zigzag miles out of their way.
— Aerodynamic improvements to jets, including vertical extensions at the tip of each wing called “winglets” that prevent drag. They’ve been around for several years but are being deployed on a wider range of planes.
— Carrying less weight inside the plane. American is replacing its 19,000 catering carts with models that weigh 16 pounds less. Southwest is testing seat covers made with lighter fabric. JetBlue chose thinner seats for its new A320s. Every pound removed from a plane saves 30 gallons of fuel a year.
— Replacing older jets faster. American, which has the worst fuel economy among U.S. airlines, is replacing aging MD80s with 737s that use 35 percent less fuel per passenger.
Airlines are cutting costs in other areas as well.
Ten years ago, salaries and benefits accounted for 39 percent of industry expenses. Now they account for 28 percent. Several major airlines filed for bankruptcy and that allowed them to renegotiate labor contracts.
But with oil at $100 a barrel and expected to rise more in the years ahead, analysts say the long-term imperative for airlines is singular: they must dramatically cut their fuel consumption.
“Either they do it,” says Darryl Jenkins of the Aviation Consulting Group, “or they go out of business.”