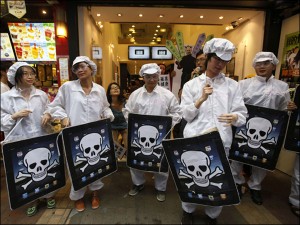
In this file photo taken Saturday, May 7, 2011, local and mainland Chinese university students, dressed as the Foxconn workers, hold mock iPads with a skeleton print outside an Apple Premium Reseller shop in Hong Kong. An explosion that occurred on May 20, 2011, at one of two factories that make Apple's new iPad 2 highlights the risks of a global manufacturing strategy that has cut costs but concentrates production in a few locations. (AP Photo/Kin Cheung, File)
Foxconn Technology Group, the contractor that manufactures Apple’s iPhones and iPads, said Friday’s blast in the western city of Chengdu killed three employees and injured 15. The Taiwanese company said production was suspended but did not respond to questions Monday about how supplies of iPads might be affected.
Foxconn said the blast was caused by combustible dust in a workshop that polished products. It said operations in workshops that do similar work at its other factories in China would be suspended pending an investigation.
Estimates by industry analysts of the impact on iPad production ranged from minimal to up to 2.8 million units in lost output. That is equal to just over half the number sold in the first three months of this year but Apple says sales are so strong it already is struggling to keep up with demand.
“There probably is going to be no impact” if production resumes as expected in the next few days, said Citigroup analyst Kevin Chang in Taipei. “If this safety inspection drags on for two or three weeks, then there will be an impact on production.”
Coming as global auto and electronics makers struggle with parts shortages caused by Japan’s March 11 tsunami, the disaster emphasized the pitfalls for companies whose global sales depend on one or two factories.
“If you are trying to do as much as you can in one place to reduce the risks of an overextended supply chain, then you are very dependent upon the safety of those one or two factories,” said David Dayton, owner of Silk Road International Inc., which manages purchasing and manufacturing in China for foreign customers.
Electronics makers such as Foxconn have flocked to China, drawn by a low-cost workforce and good infrastructure, making it the global manufacturing center for computers and consumer electronics.
All of Apple’s iPads are produced at Foxconn factories in Chengdu and Shenzhen, near Hong Kong, said Chang. But he said that is not overly concentrated in an industry in which a contractor with a single factory might supply a laptop computer sold worldwide.
Foxconn, a unit of Hon Hai Precision Industry Co., is a leader in a contract manufacturing industry that helps global electronics brands hold down costs. Chinese factories produce 80 to 90 percent of the world’s notebook computers and 50 to 60 percent of mobile phones.
Foxconn illustrates the complex web of trade and investment ties between China and Taiwan, the self-ruled island that Beijing claims as its territory.
Taiwanese companies have invested tens of billions of dollars in the mainland, despite their government’s lack of formal ties with Beijing. They make clothing, toys and other goods and are moving into higher-value electronics and computer chips.
Foxconn delivers savings for Apple, Hewlett-Packard Inc. and other customers by operating on a vast scale. It employs an estimated 1 million to 1.1 million people on the mainland in a half-dozen sprawling campuses the size of small cities.
The potential pitfalls of such massive concentration were driven home when Japan’s tsunami forced thousands of factories to shut down, abruptly cutting off supplies of key auto and electronics components. Auto factories as far away as Louisiana were forced to suspend production.
Industry analysts said the shock was likely to prompt manufacturers to reconsider supply strategies that can depend on a handful of producers in distant locations.
Contract manufacturers find China so appealing that “clients really would have to pay them extra to leave China and set up production elsewhere,” said Citigroup’s Chang.
In China, potential supply chain problems can be traced in part to companies’ decisions over the past decade to use fewer suppliers both to save money and to be able to monitor them more closely.
Customers get lower prices by placing giving more business with one company and want to watch suppliers carefully following a string of scandals over shoddy or toxic Chinese-made toothpaste, tires and other goods.
Dayton said some of his customers that buy millions of dollars worth of Chinese goods each year choose to deal with only one or two suppliers.
“The major problem is quality and consistency,” he said. “If we diversify the number of factories we work with, we are just adding headaches and adding that many more opportunities to get lesser-quality products.”
Demand for iPads is so strong that Apple’s chief operating officer, Tim Cook, said last month the Cupertino, California-based company was working through “the mother of all backlogs” on orders.
Still, Apple’s market position is so strong that it can easily ride out potential supply disruptions, said David Wolf, a technology marketing consultant in Beijing.
“A few issues on the supply chain aren’t going to hurt it now,” said Wolf, CEO of Wolf Group Asia. But he said Apple could face challenges from products such as Google Inc.’s tablet computer.
“They’ve got competitors who are running very hard to catch up,” Wolf said. “So these aren’t issues today but that will not always be the case.”
___
Associated Press writer Debby Wu in Taipei contributed.