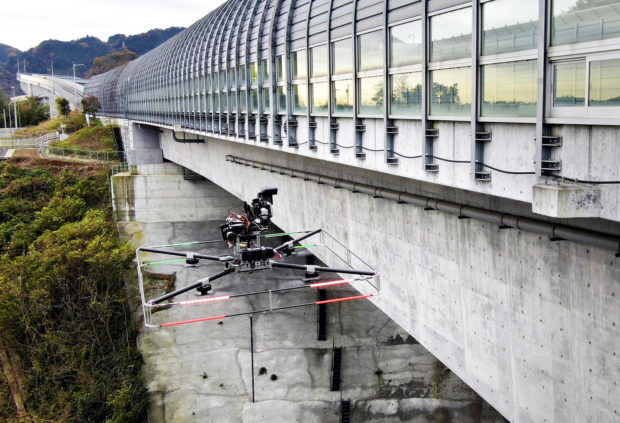
The Japan News/Asia News Network
TOKYO — The maintenance of infrastructure under the management of Japan’s small municipalities has become an issue. Last August, it was revealed that among roughly 770,000 assets such as bridges and tunnels in locations across the country, approximately 80,000 — or about 10% — have been assessed as requiring repairs within the next five years.
“Right, right … Now a little to the left,” a worker in a helmet was calling out instructions while checking a monitor under a bridge on the Metropolitan Inter-City (Ken-o) Expressway that crosses the Sagami River in Sagamihara, Kanagawa Prefecture, in early December.
Displayed on the screen was an anchor bolt, which was holding in place a noise barrier located 50 meters above the ground. Circling overhead, a camera-equipped drone was taking a series of snapshots, allowing the workers to make sure the bolt had not come loose, and to check for other defects.
Inspections of this nature would once be performed by eye, by workers standing on elevating platforms or suspended from ropes. The introduction of drones has drastically changed the way these inspections are done.
“We can now cover a wide area from multiple viewpoints,” an executive of Central Nippon Highway Engineering Tokyo Co. said.
The highway is managed by the Central Nippon Expressway Co. (NEXCO Central) Group, which began developing drones to specialize in inspection purposes in fiscal 2014.
The company turned to drones following the collapse of heavy concrete ceiling panels in the Sasago Tunnel on the Chuo Expressway in Yamanashi Prefecture in December 2012.
The accident, which claimed the lives of nine people, occurred when the anchor bolts that supported the ceiling panels gave way due to factors including the degradation of adhesives. A report by the Land, Infrastructure, Transport and Tourism Ministry pointed to inadequacies in the company’s inspection practices and maintenance regimen.
In a room at a research and development facility operated by the Kawasaki city government for start-up companies, engineers are working on a project to develop inspection robots.
In an office filled with camera- and monitor-equipped robots of various shapes and sizes, they use computers to inscribe lines on photos of a cracked concrete wall, and teach an artificial intelligence program how to identify the spots it should check in an inspection.
This project is being run by iXs Co., a company with 34 employees as of Jan. 1. iXs was founded in 1998 by Fuminori Yamasaki, whose talents had previously been displayed at robot design contests. Anticipating that aging infrastructure would become a social issue, the company pivoted to the development of inspection robots in 2005.
iXs has thus far produced over 300 unique robots, each custom-made to inspect roadways or facilities such as factories and power plants. “We’ve refined our technology by tailoring it to the public’s needs,” says Yamasaki. As labor shortages become increasingly acute, the demand for help with inspections grows, a development iXs sees as a business opportunity.
Concrete that lasts 100 years
Roads, bridges and other infrastructure assets around Japan were built at a rapid pace during the high-growth era of the 1960s and 1970s. Concrete is generally expected to show signs of degradation such as corrosion and cracking by its 50th year in service.
With the aim of doubling that life expectancy to upward of 100 years, Taisei Corp. has developed a concrete in which high-strength fiber is used in place of steel reinforcement bars. According to the company, this concrete offers the benefits of high density and reduced permeability, and is less susceptible to being penetrated by water and salt, which cause cracking and corrosion.
While this type of fiber-reinforced concrete was previously believed to be difficult to use in floor slabs for expressways because it does not easily harden, Taisei reports that as of a proof-of-concept trial held in November 2019, it has addressed most of the design’s weak points. Of the company’s plans for a commercial roll-out in the 2021 fiscal year, “We are hoping to speed that up as much as we can,” says Hiroyuki Musha, who is in charge of developing the new product. Technological innovation may prove to be a secret weapon in municipalities’ efforts to formulate strategies for dealing with aging infrastructure.
Preventive maintenance
According to an estimate by the transport ministry, the costs associated with maintaining and improving Japan’s roads, airports, dams, sewers and other infrastructure had climbed to approximately ¥5.2 trillion a year as of fiscal 2018.
If that infrastructure deteriorates due to age, the costs will grow even further. Taking a “corrective maintenance” approach, doing repairs on facilities only after issues such as cracking or corrosion emerge, would result in those costs surpassing the ¥10 trillion mark in fiscal 2048.
On the other hand, the same report states that taking a preventive approach to maintenance, performing repair work before problems occur, would limit costs to an approximate maximum of ¥6.5 trillion within the same time frame.
However, local governments are faced with economic difficulties, and roughly 80% of the bridges that had been deemed in need of repairs according to inspections performed up to fiscal 2018 have yet to be serviced.
In the central government’s initial budget for fiscal 2020, a targeted system of assistance payments for repairs on facilities with particularly pressing needs will be created. The government’s intent is to move ahead with the transition to a preventive approach to maintenance.